Additive Manufacturing in Warfare
The following is a brief overview of the dynamics of additive manufacturing (AM) for military purposes as a means of industrial and (unconventional) decentralized production of armaments and equipment. The latter has developed particularly rapidly, both in an industrial setting and in the hobbyist sector, leading to new security risks. Currently, AM is sparsely regulated, and innovative approaches are needed to tackle the challenges of global proliferation of self-manufactured 3D-printed armaments. Moreover, dual-use regulations would make it easier to control the proliferation of industrial machines that are capable of producing security-relevant technology.
Enabling a broad set of applications, additive manufacturing (AM)—commonly referred to as 3D printing—has sparked the interest of a whole spectrum of actors. These range from hobbyists to engineers across industries, but also include nefarious actors utilizing the technology for criminal purposes. The use of AM for illegitimate purposes has thus become an area of concern for national and international security. AM comprises a set of enabling technologies that allow for the production of weapons or other military and security-relevant equipment, including many different types of sometimes problematic products. As a result, these technologies are characterized as dual use.1 Currently, the main threat is posed by non-state actors’ ability to produce items that endanger public security, i.e., through 3D printed firearms, or other security relevant items, e.g., parts to assemble improvised explosive devices (IEDs) or other weaponizable items. While some of these threats have already materialized, demonstrated by the ever increasing number of sophisticated 3D printed guns seized by police,2 the effects of AM on international security and stability have been less pronounced.
This might change though, given the influx of 3D printed items in current theaters of war, such as in Ukraine and Myanmar. Both top-down and decentralized bottom-up development and distribution of additively manufactured items can be observed, shaping the material realities in areas of conflict. The following is a brief overview of the dynamics of AM first, as a military capability for improving the logistical resilience of troops and second, as a means for (unconventional) decentralized production of armaments and equipment. Finally, the implications for arms control and regulation are explored with regard to the technological environment of AM in warfare, which is characterized by a narrowing gap between active combatants and the civilian sphere.
Technical Background
The basic technological process behind AM is the creation of items, layer by layer, following a 3D digital model or design. In contrast to conventional manufacturing processes, such as forming and cutting, or milling, only the material needed for the final volume is used, resulting in less scrap material. Cohesion between layers is ensured through the melting of boundary layers or through chemical processes. The international standard (DIN EN ISO/ASTM 52900) differentiates between seven different categories of AM, which are further divided into diverse subcategories.3
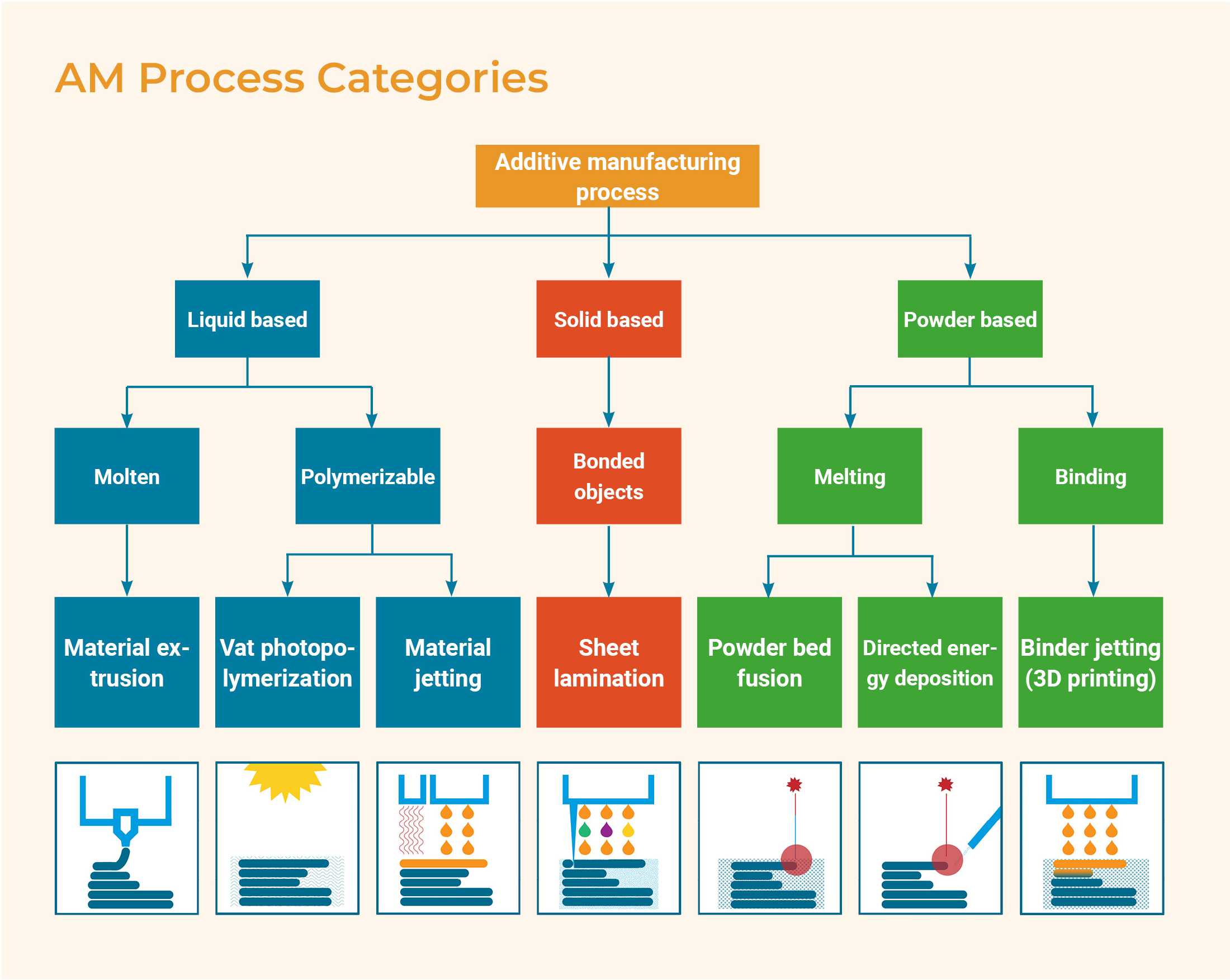
As is the case with most manufacturing processes, which material and process are used to produce an item strongly depends on the intended use case. A broad range of different materials can be processed, from plastic and metal to cells or even concrete. Depending on the material, specialized AM machines are used, which include relatively accessible and affordable desktop printers for home printing, technically complex and expensive industrial printers in which layers of metal powder are melted with a laser to print intricate items, and big machines that enable the production of ship propellers using as a production technique. In most cases, additional postprocessing is needed to ensure material cohesion, durability, and surface quality. All this demonstrates the diversity of AM and serves to drive the continuation of intensive research, testing, and standardization to enable new options for production. The industries that are projected to lead the integration of AM as part of their production chains are aerospace, medical, and tooling.4
Additive Manufacturing in Active Theaters of War
Today there are a growing number of reports on the ever-increasing variety of ways in which AM is being used in armed conflicts. Most information about these technological developments derives from social media and posts by combatants or journalistic articles, either discussing self-made armaments and equipment or detailing new use cases developed by the arms industry. From these reports on the utilization of AM in theaters of war, a dichotomy is evident: on the one hand there are conventional military and industry actors developing AM as a military capability to mature new products and improve the readiness and responsiveness of the armed forces. On the other hand, there are the decentralized, bottom-up efforts of diverse, often globally connected non-state actors who design and produce technical military equipment—in many cases free of charge—and distribute it directly to the combatants. Regardless of the origin of the supply, the common goal is to develop cost-efficient production processes, bridge gaps in the supply chain, or enable access to goods that would otherwise be inaccessible.
Additive Manufacturing as a Military Capability: Conventional State-Sponsored Supply and Distribution for Increased Resilience
As part of military aid, the United States has supplied unspecified 3D printers to the Ukrainian Armed Forces (UAF) enabling the troops to restock firing pins for the M777 howitzers and other items close to the frontlines.5 Many platforms, such as the howitzer, are challenging to repair and maintain without specific expertise. To address this, the US has devised a program offering such expertise to the UAF remotely to allow a fast return of the platform to the frontline.6 This is one example of how AM can be used in the initial stages of attrition warfare, in which conventional supply lines are yet to be established. It is also an example of the state of the art of AM as a military capability which can already be rapidly fielded. The aim of improving this capability is to increase responsiveness, readiness, and autonomy in the theater of war, including in the later stages of the fighting.7 These benefits are not limited to active combat zones, but apply more generally to material management and logistics in the armed forces. As the systems are often in use for several decades, the original equipment manufacturers (OEMs) sometimes discontinue the production of spare parts. Additive manufacturing can be used to produce such legacy parts, thus extending the lifespan of these systems. Professionalizing the capability of producing items in situ is also envisioned as a way to increase efficiency in military camps and bases by making them less dependent on on-time deliveries of replacement parts from their country of origin8 and ultimately cutting the costs associated with material dependencies on the OEMs.9 A similar dynamic applies to naval forces, as these are cut off from supplies during missions and only have access to tooling and parts on board.10 In summary, AM in warfare has the potential to enable rapid, timely, and on-demand production of parts. A broad range of applications is possible, from temporary replacement parts and normal wear and tear to maintenance of legacy systems. Additive manufacturing technologies allow for greater material independence in situ, enabling the printing of small quantities of parts and fast materialization of customized parts for medical use cases. Taken together, all these applications aim to increase the resilience of the armed forces.
In addition to AM’s application in active theaters of war, the arms industry is interested in utilizing these technologies more generally. New developments and AM technologies hold the promise of constructing new lightweight products and cutting production costs in line with the overall goal of improving military logistics and increasing production efficiency.11
Additive Manufacturing in Primary Production of Armaments and Equipment: The Growing Role of Non-State Actors
Apart from its top-down integration in the military, AM is increasingly being used by non-state actors to produce military technology and equipment, which is partly or largely 3D printed. This development mirrors the conventional supply of armaments by the state and establishes decentralized non-state actors as developers and independent bottom-up suppliers of arms. An well-known example is the aforementioned 3D printing of firearms and other devices that could be used or refitted as weapons. Items like this are being used in the conflicts in Ukraine and Myanmar, but have also appeared in several right-wing incidents of gun violence. Around 3D printed guns, in particular, we are seeing an ever growing online community evolving, exchanging designs, best practices, and detailed information on how to build guns. Beginning with a model named the “Liberator,” a rather rudimentary design allowing for just one shot to be fired, 3D printing efforts have progressed to semi-automatic pistol-caliber carbine, such as the 9mm “FGC-9,” which consists of 80–90 percent 3D printed polymer parts. A considerable amount of experimentation with different parameters, for example raw materials, process temperature, and flow velocity is needed to achieve the material characteristics that render 3D printed firearms functional and hence dangerous. Research by national authorities has shown that such weapons come close to the performance of conventional arms and are used as such by the rebels fighting against the military junta in Myanmar.12 Thanks to the accessibility and affordability of 3D desktop printers, innovation of polymer parts is not limited to firearms but has been expanded to include new items such small drones, ammunition and bomb casings, as well as medical supplies, such as tourniquets etc.
Innovation Close to the Frontlines
In both Ukraine and Myanmar, this innovation occurred spontaneously, originating in diverse and decentralized efforts by family members, volunteers, associations, and online communities to support soldiers on the frontlines. With the ongoing conflict, these innovation, manufacturing, and distribution networks have been increasingly professionalized. In Ukraine, the government has created an innovation structure called “Brave1” to increase the efficiency of the development and innovation process that aims to facilitate experimentation and a rapid fielding of new systems. Combined with individual and collective non-state support, this has led to an environment in Ukraine in which many new actors are designing and providing 3D printed military equipment, among other things.13 Some examples are 3D printed trench periscopes, tailfins for bombs, drone bomb casings, drone launching platforms, drone grabber claws, AK magazine loaders, etc.14 With this increasing professionalization, some actors have become suppliers for the UAF, then part of the top-down supply chain. However, many actors do not operate as companies but rather as networks supplying items directly to soldiers, circumventing the top-down supply line. The result is an influx of what are often non-standardized products responding flexibly to the material needs of local units. Because supply and distribution are often decentralized, it can be assumed that access to these items differs along the frontline. The degree to which this unequal distribution has an impact on warfare is unclear, but product testing and prototyping has increasingly been normalized during the conflict in Ukraine.15 As 3D printed items are part of such developments, additional proliferation risks arise, such as the normalization of a practice of trial and error, where the burden of such experiments is borne not by the actor conducting the tests, but by the subject being tested on.16 It is clear that the do-it-yourself manufacturing and distribution of additively manufactured items for and at the frontline is a trend that will continue influencing theaters of war globally, further reducing the distance between the war zone, the fighting, the combatants, and everyone else.17
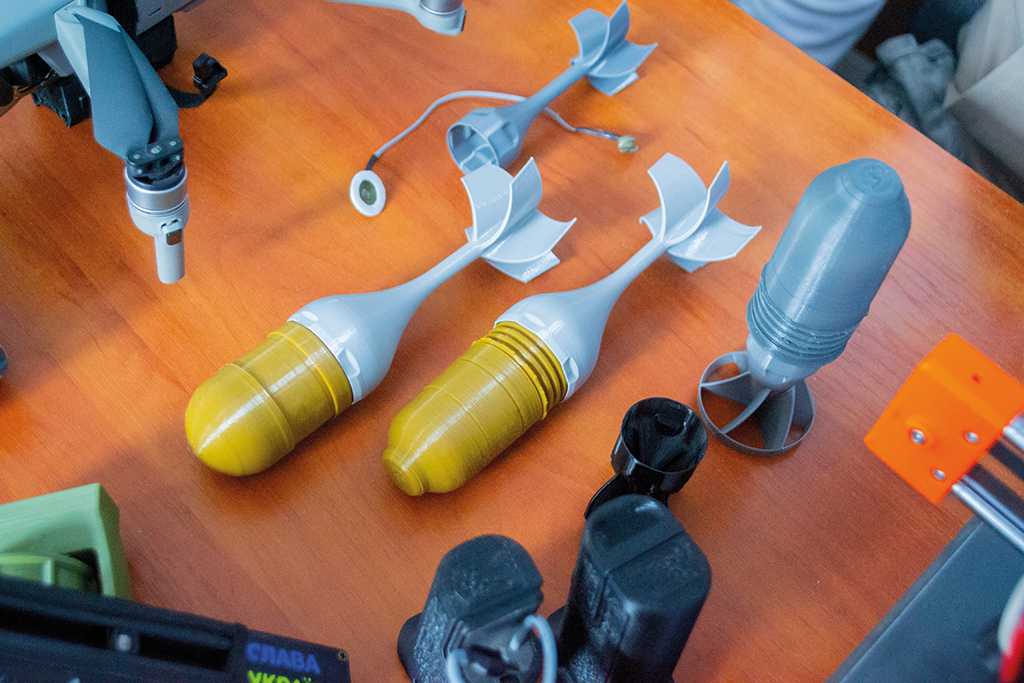
Arms and Export Control of AM Technologies
Following the premise of arms control regimes as a de-escalating tool, the main focus in this section is to evaluate the risk posed by AM technologies for stability and security. The two aforementioned trends in warfare are characterized by different dynamics and should be considered separately. The first trend, improvements in the logistical supply chain for armaments and equipment, is not expected to have any destabilizing effects warranting a closer examination for arms control purposes. However, the second trend, namely the ability to produce armaments in the form of 3D printed firearms or other equipment, such as drone components or ammunition (except the explosive matter) is concerning.
The main source of these concerns is the configuration of new actors and networks that are participating in the production of military technology. Ukraine, in particular, has seen the development of a new market for commercial actors advancing new systems that originated in civilian applications and are now being refitted for military usage.18 Together with actors with non-commercial interests who are aiding the war effort, the community of expertise on how to design, build, and distribute dual-use items adapted for military purposes is growing. This poses a proliferation risk, since it is difficult to prevent knowledge being transferred for illegitimate purposes.19 National law enforcement authorities already face considerable challenges due to the proliferation of unregistered 3D printed weapons. As expertise is shared online, it is only a question of time before innovations extend to other items, such as 3D printed rocket launchers. The same applies to the increasingly proficient construction of small drones, too, this is likely to spread from the war context to the civilian sphere.
Regulatory Framework and Nonproliferation Strategies
The risks to international security and stability posed by AM technologies, software, and raw materials are currently less pronounced. State actors that might seek to disrupt international stability are not gaining a decisive advantage through AM. Although the proliferation of AM technology can enable more efficient production of items, there is no indication that this increase in efficiency is either facilitating the knowledge and materials needed to produce weapons of mass destruction or enabling actors to significantly endanger strategic weapon and defense systems. For such systems to materialize, beyond owning the means of production, knowledge and supporting infrastructure, is needed. At this point, it is up to the German government to decide the extent to which the control of sophisticated manufacturing technology (in this case AM) and its end user is politically desired. Regarding national security, Germany has laws in place that regulate both the production and possession of weapons of war, other armaments, and the use of drones. Security risks could emanate from self-made devices if their sheer mass overwhelms the enforcement capabilities. When it comes to desktop 3D printers, which mostly print polymer parts, such as handguns or stabilization fins, proliferation control by export regulation is impossible, as these printers are technologically fairly simple, globally available, and do not need to be specifically modified to print arms. Approaches to counter the dangers of self-printed armaments are in development, however, including “poisoning” 3D designs, i.e., the proliferation of manipulated designs online that either corrupt the printer or render the print unfit for purpose. Another possible avenue for control would be to address the sale of kits that contain the nonprinted parts of these guns, such as the barrel, as this would help tackle self-made arms. These sets contain a selection of items that are freely available in hardware stores. They are curated and cater specifically for people wanting to manufacture their own handguns. Others have also suggested monitoring behavior and establishing rules for transparency and peaceful use.20 As the development and the availability of designs online will continue, capabilities in the hobbyist community and among non-state actors to make their own armaments will expand as well, circumventing law enforcement. Right-wing terrorists, in particular, have adopted 3D printed firearms as a symbol of the independence of their terror attacks.21
UN Programme of Action on Small Arms and Light Weapons
The issue of AM was part of the agenda of the Fourth Review Conference, held in June 2024, of the United Nations’ Programme of Action (PoA) to Prevent, Combat and Eradicate the Illicit Trade in Small Arms and Light Weapons (SALW) in All Its Aspects. The orally revised outcome document encourages states to share best practices to counter the proliferation of newly developed and manufactured SALW and their intangible design files and to engage with the AM industry to aid these efforts.22 Additionally, an open-ended technical expert group has been established to systematically discuss and exchange knowledge about new ways to manufacture SALW, focusing also on polymers in the production and modular SALW designs.
This international forum offers the possibility to evaluate the extent to which strategies developed for SALW are appropriate for other 3D printed items which can be used as (part of) a weapon. As the mechanisms of design and production, i.e., sharing intangible designs online and decentralized production at home, are similar to 3D printed SALW, the action points in the PoA could be applicable to other security-relevant items produced using hobbyists’ AM technologies.
Dual-Use Export Regulation
More complex and technologically sophisticated AM machines are sparsely regulated under dual-use regulations.23 One exception to this in the European Union is Spain’s national regulatory framework which addresses AM machines specifically, according to the latest EU compilation document to coordinate export controls for dual-use items (C/2023/441).24 The Spanish regulation singles out machines with the capability to print explosives. As testing for such applications is also underway in Germany, but has not yet matured, a regulatory framework that includes such applications could preempt the proliferation of this technology from Germany and other European countries and partners before it is fully developed.25
The Blurred Line Between Civilian and Military Research
The line between civilian and military use of AM is becoming increasingly blurred, mostly driven, on the non-state side, by online communities and decentralized manufacturers. This development poses security risks, some of which are already understood and some of which are yet to develop. Measures that stimulate civil-military research, such as the efforts of the German Federal Ministry of Education and Research to question the strict divide between military and civilian research26 need to address the potential of sensitive knowledge being disseminated outside the designated research institutes, companies, and universities. As German research ethics for dual-use research strongly focus on individual responsibility,27 the extent to which a regulatory framework enforces the rules for peaceful use, or relaxes them to encourage the development of new commercial military technology actors becomes a political concern.
Footnotes
-
Forge, J. (2010). A Note on the Definition of “Dual Use”. Science and Engineering Ethics, 16(1), 111–118. https://doi.org/10.1007/s11948-009-9159-9 ↩
-
Schroeder, M., Florquin, N., Fabre, A. & Varisco, A. Privately Made Firearms in the European Union. Flemish Peace Institute. https://gunviolence.eu/wp-content/uploads/2023/11/Project_INSIGHT_Emerging-Threats_DEF.pdf ↩
-
DIN Media. Additive Fertigung. https://www.dinmedia.de/de/themenseiten/additive-fertigungsverfahren ↩
-
Gebler, M., Schoot Uiterkamp, A. J. M., & Visser, C. (2014). A global sustainability perspective on 3D printing technologies. Energy Policy, 74, 158–167. https://doi.org/10.1016/j.enpol.2014.08.033; Altıparmak, S. C., & Xiao, B. (2021). A market assessment of additive manufacturing potential for the aerospace industry. Journal of Manufacturing Processes, 68, 728–738. https://doi.org/10.1016/j.jmapro.2021.05.072 ↩
-
Harper, J. (2023, September 15). Pentagon arms Ukraine with ‘industrial-size’ 3D printers. Defensescoop. https://defensescoop.com/2023/09/15/pentagon-arms-ukraine-with-industrial-size-3d-printers/ ↩
-
TOC. (2024, February 24). Ukraine’s self-repair: M777 howitzer video sparks DIY weapon fix. Bulgarianmilitary. https://bulgarianmilitary.com/2024/02/15/ukraines-self-repair-m777-howitzer-video-sparks-diy-weapon-fix/ ↩
-
Boer, J. D., Lambrechts, W., & Krikke, H. (2020). Additive manufacturing in military and humanitarian missions: Advantages and challenges in the spare parts supply chain. Journal of Cleaner Production, 257, 120301. https://doi.org/10.1016/j.jclepro.2020.120301 ↩
-
Westerweel, B., Basten, R., denBoer, J., & vanHoutum, G. (2021). Printing Spare Parts at Remote Locations: Fulfilling the Promise of Additive Manufacturing. Production and Operations Management, 30(6), 1615–1632. https://doi.org/10.1111/poms.13298; siehe S. 1628 ↩
-
Tegler, E. (2024, May 7). Navy Pays $100K To Replace Each F/A-18 Tire, 3D Printed Repairs Cuts Cost To $300. The Warzone. https://www.twz.com/sea/navy-pays-100k-to-replace-each-f-a-18-tire-3d-printed-repairs-cuts-cost-to-300 ↩
-
Hartig, S. (2023). Integrationslogik Additiver Fertigungsverfahren zur Unterstützung zeitweise autarker Systeme [Dissertation, Helmut-Schmidt-Universität/Universität der Bundeswehr Hamburg]. https://doi.org/10.24405/15016 ↩
-
Santos González, D., & González Álvarez, A. (2018). Additive Manufacturing Feasibility Study & Technology Demonstration—EDA AM State of the Art & Strategic Report. European Defence Agency. https://eda.europa.eu/docs/default-source/projects/eda-am-study-and-strategic-report_v6.pdf ↩
-
Molitch-Hou, M. (2023, August 1). Myanmar Rebels Rely on 3D Printed Guns to Fight Military Junta. 3D Print. https://3dprint.com/302100/myanmar-rebels-rely-on-3d-printed-guns-to-fight-military-junta/ ↩
-
Gosselin-Malo, E. (2024, February 22). How Ukraine’s defense companies have adapted to two years of war. Defense News. https://www.defensenews.com/global/europe/2024/02/22/how-ukraines-defense-companies-have-adapted-to-two-years-or-war/ ↩
-
Hambling, D. (2024, June 7). Volunteers Worldwode With 3D Printers Are Aiding Ukraine’s War Effort. Forbes. https://www.forbes.com/sites/davidhambling/2024/06/07/how-volunteers-worldwide-are-helping-ukraines-war-with-3d-printers/ ↩
-
Siehe 14. ↩
-
Hoijtink, M. (2022). ‘Prototype warfare’: Innovation, optimisation, and the experimental way of warfare. European Journal of International Security, 7(3), 322–336. https://doi.org/10.1017/eis.2022.12 ↩
-
Ford, M. C., & Hoskins, A. (2022). Radical war: Data, attention and control in the twenty-first century. Hurst & Company. ↩
-
Bergengruen, E. (2024, February 8). Tech Companies Turned Ukraine Into an AI War Lab. TIME. https://time.com/6691662/ai-ukraine-war-palantir/?linkId=315027696; Volpicelli, G., Melkozerova, V., & Kayali, L. (2024, 16. Mai). ‘Our Oppenheimer moment’—In Ukraine, the robot wars have already begun. POLITICO. https://www.politico.eu/article/robots-coming-ukraine-testing-ground-ai-artificial-intelligence-powered-combat-war-russia/ ↩
-
Kunertova, D. (2023). Drones have boots: Learning from Russia’s war in Ukraine. Contemporary Security Policy, 44(4), 576–591. https://doi.org/10.1080/13523260.2023.2262792 ↩
-
Favaro, M. (2024). The Impact of Emerging Technologies. In J. A. Larsen & S. Smith (Hrsg.), Arms control at a crossroads: Renewal or demise? Lynne Rienner Publishers, Inc. 199. ↩
-
Veilleux-Lepage, Y. (2021). CTRL, HATE, PRINT- Terrorists and the Appeal of 3D-Printed Weapons [Policy Brief]. International Centre for Counter-Terrorism - ICCT. https://www.icct.nl/publication/ctrl-hate-print-terrorists-and-appeal-3d-printed-weapons ↩
-
United Nations Office of Disarmament Affairs. (2024, June 28). Fourth United Nations Conference to Review Progress Made in the Implementation of the Programme of Action to Prevent, Combat and Eradicate the Illicit Trade in Small Arms and Light Weapons in All Its Aspects and the International Tracing Instrument: Draft Outcome Document. A/CONF.192/2024/RC/CRP.1.Rev3. United Nations General Assembly. https://docs-library.unoda.org/Programme_of_Action_on_Small_Arms_and_Light_Weapons_-Review_Conference_ (2024)/CRP.1.Rev3_RevCon4_Draft_Outcome_Document_Orally_Revised_CLEAN_0.pdf ↩
-
Additive manufacturing is only mentioned in one section of the EU Dual-Use Regulation as an additional feature of a machine. See (EU) 2021/821, section 2B001, Note 4: “A machine tool having an additive manufacturing capability in addition to a turning, milling or grinding capability must be evaluated against each applicable entry 2B001.a.,.b. or.c”. https://eur-lex.europa.eu/legal-content/EN/TXT/PDF/?uri=CELEX:02021R0821-20231216&qid=1718280529662 ↩
-
Europäische Union. (2023, October 20). Compilation of national control lists under Article 9(4) of Regulation (EU) 2021/821 of the European Parliament and of the Council of 20 May 2021 setting up a Union regime for the control of exports, brokering, technical assistance, transit and transfer of dual-use items (C/2023/441). Official Journal of the European Union. https://eur-lex.europa.eu/legal-content/EN/TXT/PDF/?uri=OJ:C_202300441 ↩
-
Zhang, J., He, K., Zhang, D., Dong, J., Li, B., Liu, Y., Gao, G., & Jiang, Z. (2022). Three-dimensional printing of energetic materials: A review. Energetic Materials Frontiers, 3(2), 97–108. https://doi.org/10.1016/j.enmf.2022.04.00; Muravyev, N. V., Monogarov, K. A., Schaller, U., Fomenkov, I. V., & Pivkina, A. N. (2019). Progress in Additive Manufacturing of Energetic Materials: Creating the Reactive Microstructures with High Potential of Applications. Propellants, Explosives, Pyrotechnics, 44(8), 941–969. https://doi/10.1002/prep.201900060 ↩
-
Bundesministerium für Bildung und Forschung. (2024). Positionspapier des Bundesministeriums für Bildung und Forschung zur Forschungssicherheit im Lichte der Zeitenwende. Bundesministerium für Bildung und Forschung. https://www.bmbf.de/SharedDocs/Downloads/de/2024/positionspapier-forschungssicherheit.pdf?__blob=publicationFile&v=1 ↩
-
Jakob, U., Kraemer, F., Kraus, F., & Lengauer, T. (2024). Applying Ethics in the Handling of Dual Use Research: The Case of Germany. Research Ethics, 0(0). https://doi.org/10.1177/17470161241261044 ↩